Logistics Key Performance Indicators or KPIs are a technique for businesses for comparing their own enactment against industry benchmarks. It is an objective and practical measurement of progress, either:
- For achieving a predetermined goal, or
- In contrast to a requisite standard of performance
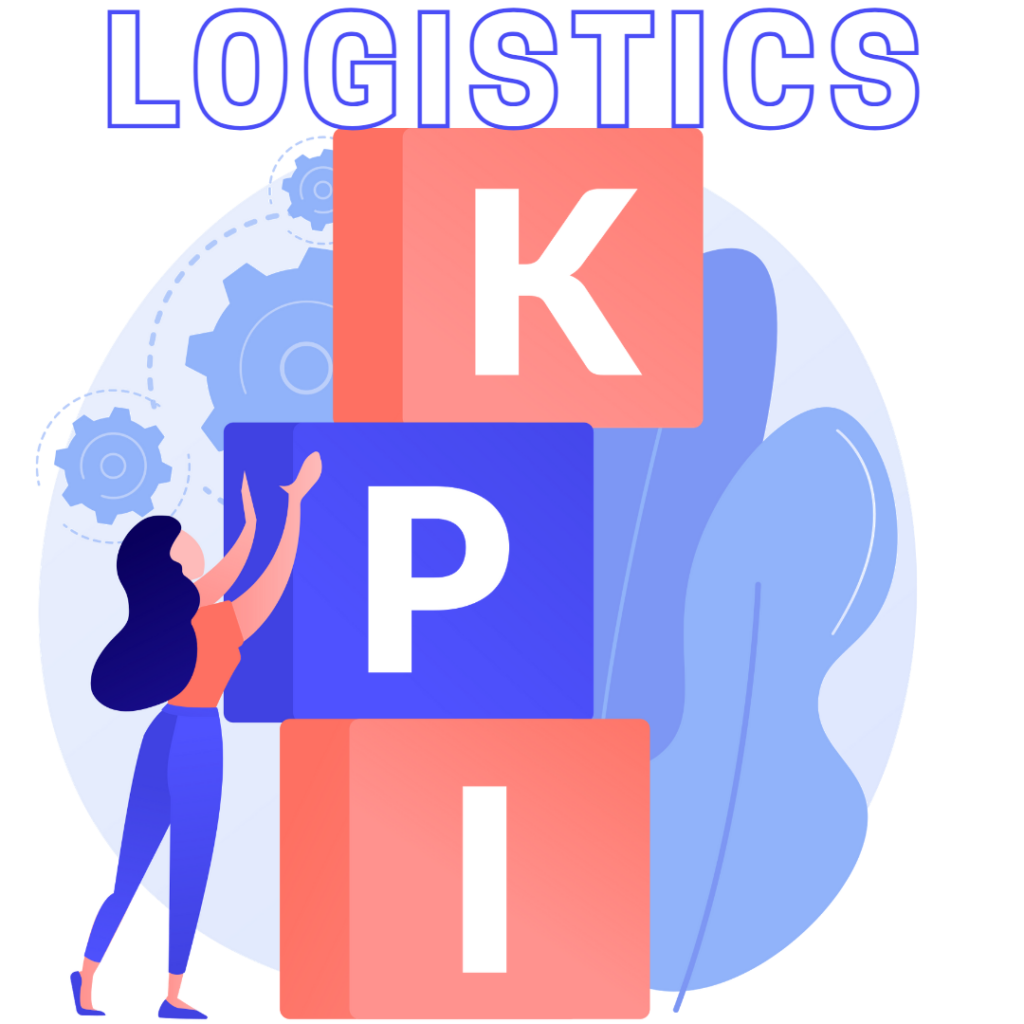
By tracing KPIs, businesses have important data that aids them to improve their operations. This data will mark any fluctuations and allows negative variations to be recognised and addressed efficiently.
Setting Up Logistics KPIs
Setting up logistics KPIs requires to first define the company’s logistics goals ensuring that these goals are “SMART”: specific, measurable, achievable, relevant and timely.
These goals will further help in understanding what is required from the KPIs and support in adjusting business processes for improvement. Break the KPIs for each stage within the supply chain that mark the company’s potential for improvement in the industry. Some of the important KPI’s that need to be considered are:
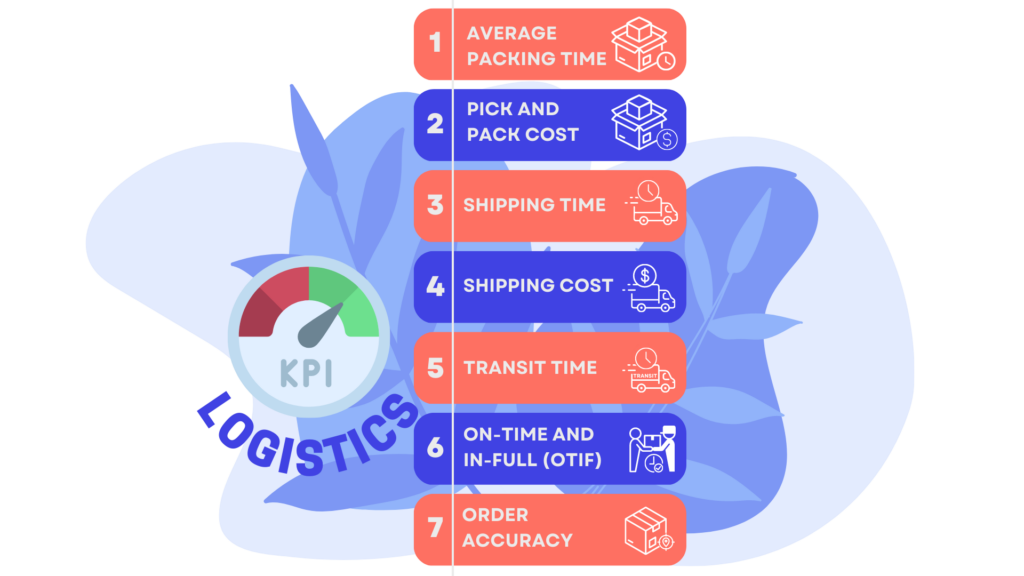
Average packing time: is the average time that is taken for a product to be picked up and get packed. Calculating this KPI regularly will help in comparing the employees’ productivity over time.
Pick and pack cost: It helps to measure the picking cycle time, the productivity, and the accuracy, as the cost transparency will help to understand the financial impact of changes in the related metrics’ values.
Shipping time: is the amount of time taken by the companies for shipping an order on or before the date requested. This metric is important for achieving customer satisfaction.
Shipping Costs: This metric helps in tracking the shipping costs per unit and identifies even the slightest changes in the set budget.
Transit time: This refers to the total time taken, right from pick up to the freight delivery at the recipients’ location. It helps in comparing the estimated transit time and inspect the carrier’s performance, to create an optimum transit time, while evaluating any possible delays that might prevent on-time deliveries.
On-Time and In-Full (OTIF): This is a customer-centric KPI that measures on-time delivery in its complete condition. It represents the number of orders to be delivered as per the schedule and the quantity specified. It calculates the amount of times the customer got what they purchased and if it was delivered within the promised time.
Order accuracy: it determines the total volume of the inventory on-hand that are shipped and delivered without any inaccuracies and identifying errors in the form of unsuccessful deliveries, incorrect orders, damaged, or returned goods.
Key points to remember while setting up the KPIs
Lorem ipsum dolor sit amet, consectetur adipiscing elit. Ut elit tellus, luctus nec ullamcorper mattis, pulvinar dapibus leo.Here are some important points that are required to be kept in mind while setting up KPIs for business operations:
· Prioritization of the procedures and operations that are important.
· Making the KPIs relevant.
· Choosing simple, achievable KPIs instead of complex targets.
· Monitoring the performance elements of the chosen metrics.
· Focusing on the activities that help the staff to give a better performance.
· Understanding the industry KPIs before making new standards
Conclusion
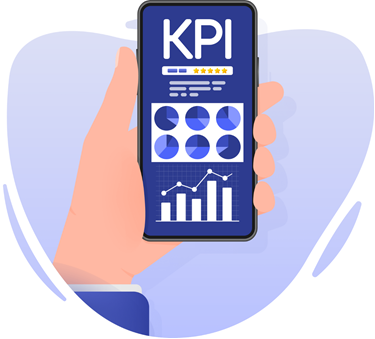
Tracking KPIs provide with a strategic vision for the overall goal and performances throughout the course of time, identifying trends, and finding key enhancement points that will benefit the business.
Aiming for the right goal will further help in using the available resources and time more efficiently for reach bigger heights.